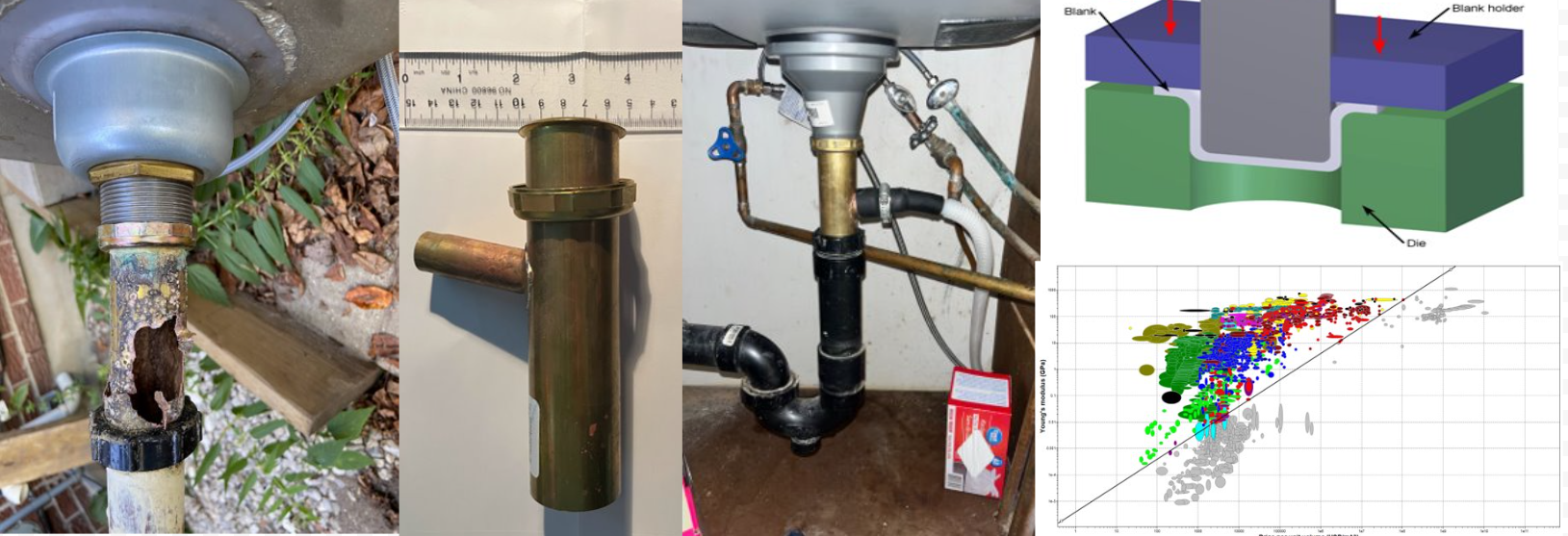
Failure Analysis of Dishwasher Tailpiece 850A for OS&B
This failure analysis project was completed as a collaboration between OS&B, a major plumbing fitting manufacturer, and my Mechanical Engineering project group at the University of Waterloo. This model of dishwasher fitting was a high warranty claim product for the company due to corrosion concentrated at the brazed connection. The analysis was completed as coursework for ME 230 and presented to OS&B managment.
Manufacturing Process
The first step in our analysis was understanding the manufacturing process from start to finish. I talked with the company’s engineers and collected material data sheets to determine the baseline for analysis.
Brass stock is cut into pucks.
The pucks are die-pressed along a shaft. The force of the press forces the brass into a tubular shape.
The cold-pressing motion imparts cold work on the brass, making it stronger, but more brittle and prone to cracking. The tubes are then annealed to remove internal stresses.
The end is cut off and a hole is punched in preparation for the tee.
The “tee” is then brazed into the main tube.
Brass Stock Material Composition:
62-62.5% Cu, 35% Zn, 1.5-2% Mn, 0.8-1% Si
Corrosion Analysis
The part was discovered under a kitchen sink corroded to failure at the soldered joint. The fitting is shown installed with signs of corrosion visible.
The fitting is seen in its final failed state. Between January 2022 and September 2022 considerable acceleration of corrosion was observed.
Given that a 97% tin solder is used in the manufacturing of the part, there is considerable risk for galvanic corrosion around the tee joint. Referencing the standard hydrogen-electrode referenced cell potentials listed in Table 1, the cell potentials can be calculated for the joint region between both Copper and Silver, and Zinc and Silver in Table 2.
Both copper and zinc have high cell potentials with tin and are thus at risk of galvanic corrosion. Additionally, the fitting is subjected to a strong electrolyte in the form of sink/dishwasher wastewater in its service environment adding to the corrosion risk. The NACE Corrosion Engineers Reference book outlines material combinations that are at high risk for corrosion in Figure 3. (Accessed from structx.com)
The combination of brass and tin is highlighted as high risk for corrosion when subjected to electrical contact and electrical presence such as the environment of interest.
Dezincification and Pitting Corrosion
Dezincification is another primary cause for failure. Dezincification is type of dealloying in which zinc is selectively leached from the alloy due to it’s high reactivity. The zinc particles come out of solid solution with copper, leaving behind a porous copper microstructure. This significantly reduces the structural integrity of the material leading to regions of weakness and ultimately failure. Dezincification comes with many visual indicators including pink/copper-coloured regions, white deposits of zinc carbonate (also known as meringue), and various copper compounds shown in Figure 4. In this instance, layer type dezincification around the failure surface and plug-type dezincification was observed.
A few things accelerated the dezincification:
Presence of chlorides in the water (often from dishwasher detergent and salt/NaCl found in food waste). At high enough Cl- concentrations the ZnO , CuO, and Cu2O passive layers are broken due to the formation of CuCl2- ions which drastically increases the rate of dezincification corrosion.
Oxygen starvation cells. Dissolved oxygen is necessary for the formation of oxygen starvation cells which are responsible for crevice and pitting corrosion. A high concentration of dissolved oxygen allows the creation of a greater concentration difference and therefore a greater cell potential according to the Nernst equation.
Electrolyte stagnation causes crevice corrosion and pitting. This is more likely to occur in low flow rate conditions and especially with stagnant water. Furthermore, this source discusses the importance of avoiding flow rates below <0.5m/s to avoid debris from settling which can initiate pitting and crevice corrosion.
Crevice Corrosion
Crevice corrosion is a very common cause of failure in parts ranging from automotive to exterior construction to plumbing applications. When small gaps or “crevices” are present in electrolyte rich (usually damp) environments, oxygen levels are reduced causing oxygen starvation cells. This is observed in the part of interest with gaps between the main drainpipe and the soldered dishwasher connection on both the interior and exterior of the pipe as seen in Figure 5.
Material Selection
The goal was the select a material that improves corrosion while adhering to all requirements and constraints set by the initial manufacturer.
Cost. Must be < $24.99
Strength. Must adhere to installation and service life loads.
Geometric constraints. Must be the same dimensions.
Must adhere to building and fire codes.
Must be reasonably manufacturable.
First, I derived a relationship between cost and material performance and durability (strength).
Then, using Ansys Edupak, I created an Ashby plot for Young’s Modulus and Price per unit volume. By subbing in the constraints into the above relationship, I was able to create a cut-off line for materials that satisfy both conditions. Then by filtering by other requirements such as manufacturability, and corrosion resistance, I was able to make a short list of acceptable materials
The MPI analysis resulted in six final materials. By weighing the pros and cons of these materials, I was able to select a material with improved material properties, corrosion resistance, and was able to reduce the material cost by 14%.
Two material recommendations were made to OS&B. First was a brass material with an decreaed Zn content. this was immune to dezincification yet was lightly less stiff. Second was a 20% Zn brass with additional alloying elements for corrosion resistance.